The Ultimate Guide To Buy Aluminum Welding Wire
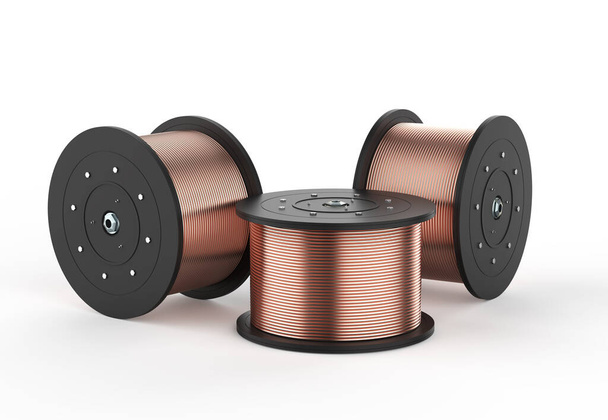
The Ultimate Guide To Buy Aluminum Welding Wire
Do you want to know more about aluminum welding wire? Look no further! In this final guide, we will explore the inside and outside of aluminum welding wire, its properties, and types, and how to use it in various welding processes. We will also cover the best methods of welding with aluminum wire, how to choose the right Wire for your project, and the necessary safety precautions. So, let’s dive in!
What is Aluminum Welding Wire?
One kind of filler metal that’s utilized to join aluminum components during the welding process is aluminum welding wire. It is essential in industries such as automotive, aerospace, and construction, where the lightweight and corrosion-resistant properties of aluminum are highly valued.
Properties of Aluminum Welding Wire
Aluminum welding wire is a great option for welding aluminum products because of its many special qualities.
- Light weight: aluminum is a light metal, making it easy to handle and transport.
- Corrosion resistance: aluminum welding wire is naturally resistant to corrosion and corrosion, which ensures the longevity of welded components.
- High electrical conductivity: aluminum has excellent electrical conductivity, making it suitable for electrical applications.
Common Types of Aluminum Welding Wire
There are numerous popular varieties of aluminum welding wire, such as:
- 4043: it is a versatile and widely used aluminum welding wire with excellent fluidity and low sensitivity to breakage.
- 5356: a strong wire with high tensile strength, suitable for high-strength aluminum alloys.
The Aluminum Welding Process
There are two primary processes of welding aluminum using aluminum welding wires: gas metal arc welding (GMAW) and gas tungsten arc welding (GTAW).
Gas Metal Arc Welding (GMAW)
Aluminum welding is frequently done using GMAW, sometimes referred to as metal inert gas (MIG) welding. It uses continuous aluminum welding wires through the welding gun, which creates an electric arc between the wire and the base metal. The heat generated by the arc melts the wire and the base metal, forming a strong joint when the molten material cools and solidifies.
Gas Tungsten Arc Welding (GTAW)
GTAW, or tungsten inert gas (TIG) welding, is another popular method for aluminum welding. To generate an arc between the electrode and the base metal, it makes use of a non-consumable tungsten electrode. The aluminum welding wire is manually inserted into the arc to form the Weld pool, which connects the base metal components
Choosing the Right Process
To decide which welding process is best for your project, consider factors such as material thickness, desired Weld appearance, and productivity requirements. GMAW is generally faster and more efficient, while GTAW provides greater accuracy and control over weld appearance.
Selecting the Right Aluminum Welding Wires
Choosing the appropriate aluminum welding wire for your project is important to ensure a strong and durable Weld. Consider the following factors:
Base Metal Compatibility
Choose a welding wire compatible with the aluminum alloy you are working with. Compatibility ensures proper Fusion and reduces the risk of weld defects.
Wire Diameter and Material Thickness
Choose the right wire diameter based on the thickness of the material you are welding. Thicker materials require larger wire diameters for proper penetration and Fusion.
Preparation for Aluminum Welding
Proper preparation is essential for successful aluminum welding. Here are some key steps:
Cleaning the Aluminum Surface
Clean the aluminum surface to remove any dirt, grease, or oxides that contaminate the Weld. Use a stainless steel brush or suitable cleaning solution to ensure a clean surface.
The Correct Way to Store and Handle Aluminum Welding Wires
Place the aluminum welding wire in a dry, cool place to prevent moisture absorption and contamination. Take care when handling the wire to prevent scratching the surface, since this could lower the quality of the weld.
Best Practices for Aluminum Welding
Follow these best practices to ensure a high-quality aluminum weld:
Welding Techniques
To ensure a smooth and uniform weld bead, use proper welding techniques, such as maintaining a consistent travel speed and torch angle.
Avoiding Common Aluminum Welding Problems
Some common issues in aluminum welding include porosity, breakage, and insufficient penetration. To avoid these problems, ensure proper preparation, use the right welding wire, and apply proper welding techniques.
Safety Precautions for Aluminum Welding
Safety is paramount when working with aluminum welding wire. Here are some essential safety precautions:
- Wear protective gear: use appropriate safety gear, such as welding helmets, gloves, and flame-resistant clothing.
- Ensure proper ventilation: welding smoke can be dangerous, so ensure adequate ventilation in your workplace.
- Use a fire extinguisher: keep a fire extinguisher nearby for emergencies.
Conclusion
This ultimate guide to aluminum welding wire provides an overview of the different types of aluminum welding wire, welding processes, and factors to consider when choosing the right Wire for your project. By following best practices and safety precautions, you can achieve high-quality, durable welds with aluminum welding wires. With the right tools and techniques, you will be on your way to mastering the art of aluminum welding.
Read More ( Click Here )